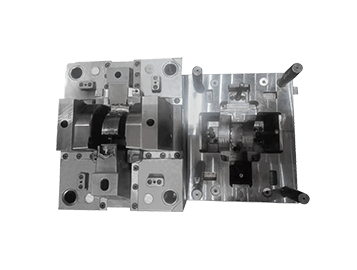
Die casting molds started out and upgraded from sand casting but it casts product with high mechanical performance than traditional casting and already evolved to variety of appliance with different material. Traditional casting principle is that filling molten metal into a mould that conventionally made by sand, salt or metal. After that it had gradually evolved to pressure die casting. In this way, the die-casting machine squeezes the molten metal into a mould cavity under high pressure and then holding metal material under pressure during solidification. Finally taking out the casted part from tooling after cooling. This kind of molds is suitable for very high rate production because of the fast solidification and automatic mold running under controlled of die casting machine. Many zinc, aluminum, magnesium, copper and it’s related alloys are cast using this method. Especially for zinc and aluminum alloys casting that extensively used to all kinds of industries, such mechanical, automotive, electrical, sport, toy fields.
In the two decades, we have been offering die-casting method and tooling service for clients from different industries, At Mold World our experienced engineers work with our customers to ensure the tooling design and manufacture are optimized for consistent quality and competitive cost.
we use cast simulation software(i.e. Flow-3D)which allows us to analyze the mold flow to assist tool design. We know precisely how to eliminate mold and casting process defects like air bubbles,porosity, entrained air (air trapping), and surface cold mark & shuts.
Learn more